1.1. МЕТАЛЛЫ
Металлами называются простые вещества, которые в обычных условиях характеризуются наличием нескольких отличительных признаков:
- высокой теплопроводностью и проводимостью электрического тока;
- ковкостью;
- пластичностью;
- кристаллическим строением на атомарном уровне, а потому имеет высокие прочностные показатели;
- температурой плавления. По этому признаку они делятся на тугоплавкие и легкоплавкие.
Сплавами называются материалы, полученные из двух и более веществ путем их нагревания свыше температуры плавления.
Металлы классифицируются следующим образом:
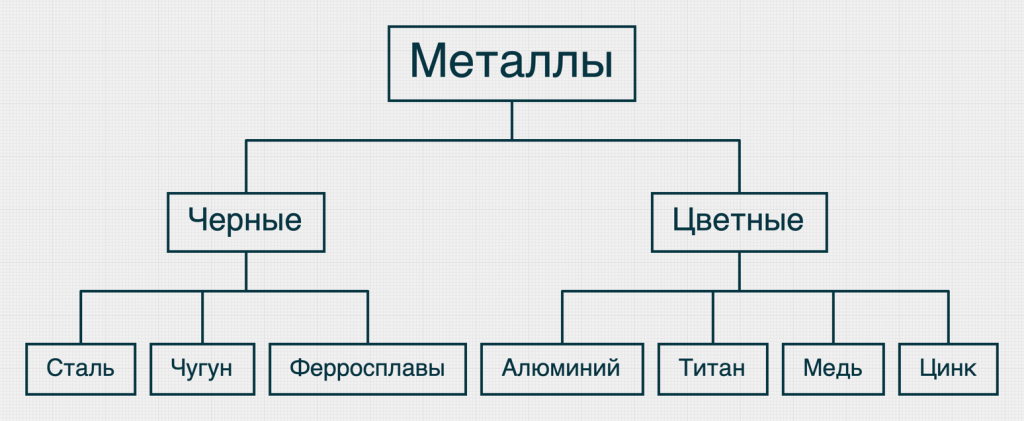
Сталь характеризуется содержанием углерода до 2.14%; чугун — содержанием углерода свыше 2.14%.
Ферросплавы – это сплавы железа с кремнием, хромом, марганцем, никелем и некоторыми другими элементами.
К цветным металлам относятся все остальные металлы и их сплавы.
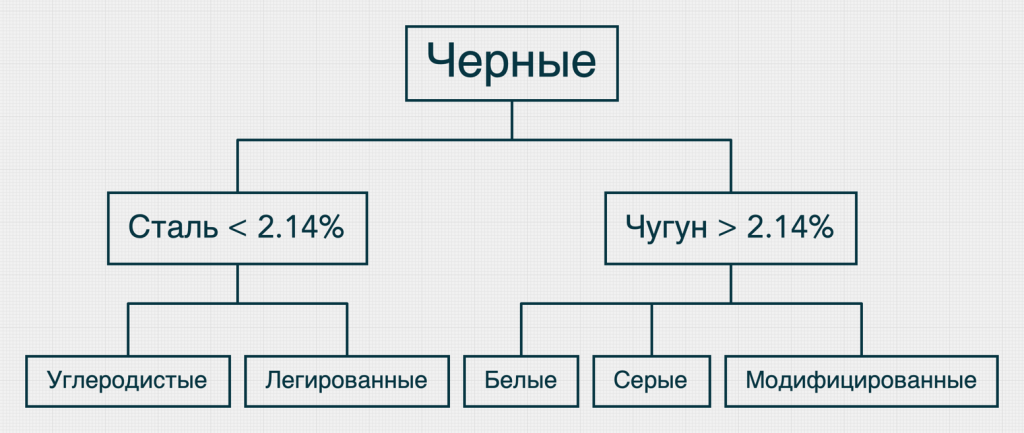
1.2. СТАЛИ
Стали классифицируются по:
- химическому составу
- назначению
- способу производства
- формообразованию
- по степени раскисления
Классификация стали по химическому составу
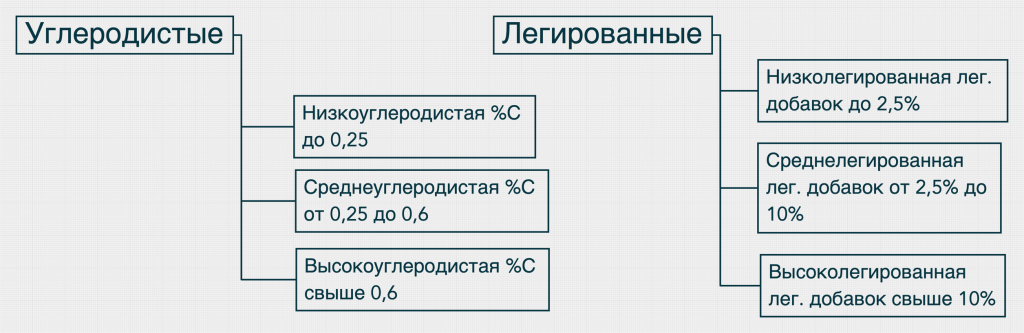
По назначению стали делятся на
- конструкционные,
- инструментальные,
- стали специального назначения.
По способу производства (по технологии получения)
-
- электрические
- мартеновские
- кислородно-конвертерные
По степени раскисления классифицируются:
- спокойные
- полуспокойные
- кипящие
Конструкционные — это углеродистые или легированные стали, содержание углерода в которых не превышают 0.5 — 0.6%. Они обладают высокой предельной прочностью. Применяются для возведения различных конструкций промышленного, военного и бытового назначения.
По применению стали подразделяют на:
- строительные стали — это стали со средним содержанием углерода. Применяется для выпуска широкой номенклатуры различных строительных металлоконструкций, фасонных и листовых профилей, труб, уголков и т.д. ;
- арматурные стали – стали, предназначенные для армирования бетонных блоков и готовых конструкций из бетона и изготавливаются в виде стержней или проволоки большого диаметра;
- котельные стали — стали используют для выпуска котлов и цилиндров, а также прочих сосудов и арматуры, которым предстоит работать в условиях повышенного давления при различных температурных режимах;
- автоматные стали — стали, которые легко обрабатываются и легко поддаются резанью;
- подшипниковые стали — стали, отличающиеся высокой прочностью и огромной устойчивостью к износу (истиранию).
В инструментальных углеродистых сталях содержание углерода колеблется от 0.7% до 1.5% . Эти стали обладают высокой прочностью, устойчивы к факторам износа и предельно высоким температурам. Они применяются
в точном машиностроении, изготовлении инструмента, медицине, в научной сфере, в отраслях, где требуется повышенная прочность и точность.
Легированные стали — это стали, в состав которых входят, кроме железа и углерода, еще некоторые искусственно добавляемые легирующие присадки (хром, никель, молибден, вольфрам, титан и др.). Кроме этих материалов в легированные стали могут входить марганец и кремний. Их содержание не превышает 0.8% — 1.2%.
Легированные стали делятся по количеству присадок на :
- Низколегированные стали — стали с низким содержанием присадок не более 2.5% .
- Легированные стали — стали с содержанием легированных присадок от 2.5% до 10% .
- Высоколегированные стали с особыми свойствами — стали с высоким содержанием легированных присадок, более 10% .
Легированные стали по назначению делятся на:
- Легированные конструкционные стали. Они используются в машиностроении, возведение зданий и прочих конструктивных сооружений, а также в промышленности. Из этих сталей делают мосты, самолеты, ракеты, оборудование для высокоточной промышленности.
- Легированные инструментальные стали используются для изготовления режущих инструментов (например, токарные резцы), а также высокоточных измерительных приборов и инструментов. Из них делают штампы для горячего и холодного проката.
- Легированные стали специального назначения. Это стали имеющие специальные свойства. Это жаропрочные стали, жаростойкие стали, стали с высокой прочностью, нержавеющие стали и др. Применяются для изделий, работающих в сложных условиях (турбины для двигателей, печи для выплавки металла).
Коррозионная стойкость стали
Углеродистые и низколегированные стали обладают невысокой коррозионной стойкостью в большинстве природных и промышленных сред и требуют соответствующих мер по защите от коррозии .
Это происходит потому, что на углеродистых и низколегированных сталях анодный процесс протекает без существенного торможения и практически без возникновения пассивного состояния. Катодный процесс харак- теризуется малым торможением реакции восстановления кислорода и существенным торможением за счет
ограниченной доставки кислорода в зону катодной реакции. Продукты коррозии железа также слабо тормозят коррозионный процесс вследствие непрочности сцепления с основным металлом и их частичности растворимо- сти в воде.
Содержание в углеродистой стали таких компонентов как углерод, марганец, кремний, фосфор, медь не имеет существенного влияния на скорость коррозии. Примеси серы и азота выше допустимых концентраций могут ускорять коррозионный процесс.
В последнее время наблюдается тенденция к увеличению использования низколегированных сталей с небольшим (2 – 3%) содержанием хрома, марганца, никеля, меди и кремния. Применение таких сталей позволяет существенно уменьшить металлоемкость конструкций и сооружений, трудоемкость и улучшить их технические характеристики. Однако использование легированных добавок в таких количествах практически не влияют на коррозионную стойкость сталей.
Прокатная окалина оказывает большое влияние на скорость коррозии. Она имеет высокую электропрово- дность, а ее стационарный потенциал в морской воде на 0,3 – 0,5В более положителен, чем потенциал стали, причем эта разница наибольшая для сталей, легированных хромом и медью. В связи с этим в процессе подго- товки поверхности перед окрашиванием прокатную окалину обязательно надо удалять . Если на поверхности стали присутствует окалина или остатки краски, имеются условия дифференциальной аэрации и механические нагрузки, то это способствует возникновению язвенной коррозии, скорость которой может составлять до 1,0 мм в год.
Коррозионностойкие (нержавеющие) стали – это металлические сплавы, которые обладают повышенной устойчивостью к коррозии в различных климатических и атмосферных условиях, а также в соленой и пресной воде, в некоторых газовых сферах, кислотах и щелочах.
Коррозионностойкие или нержавеющие стали способны противостоять различным видам химической и электрохимической коррозии. Основным химическим элементом, который обеспечивает антикоррозионную устой- чивость металла, является хром . Этот элемент сам по себе обладает высокими антикоррозионными свойствами, при добавлении в сплав в определенных процентных отношениях он образует защитную пленку на поверхности металла, которая и является основной антикоррозионной защитой. Чем выше содержание хрома, тем больше увеличивается способность нержавеющей стали противостоять коррозии в различных средах.
Другим элементом, который обеспечивает антикоррозионные свойства, является никель. Как легирующий элемент, никель вводится в металлический сплав с определенным содержанием углерода и хрома и способствует образованию твердых прочных связей, а также усилению защитных свойств. Стали с высоким содержанием никеля особенно распространены в среде, где необходимо предотвратить появление межкристаллитной коррозии. Помимо хрома и никеля, повышению антикоррозионных свойств способствуют такие элементы, как медь, молибден, марганец, алюминий, кремний. В качестве специальных стабилизирующих элементов часто вводят титан и ниобий. Титан обеспечивает повышенную стойкость к межкристаллитной коррозии.
Различие в коррозионном поведении различных марок сталей проявляется главным образом в сварных соединениях. Это определяется разностью электродных потенциалов трех элементов сварного соединения: основной металл, сварной шов и зона термического влияния. Выбор сварочных электродов и технологии сварки производится с таким расчетом, чтобы три указанные элемента имели приблизительно одинаковые потенциалы
1.3. ЧУГУНЫ
Чугуны — это сплав железа и углерода, содержание углерода в котором колеблется от 2.14% до 6.67%.
Они квалифицируются по химическому составу на:
- Белые чугуны (БЧ). Они характеризуется тем, что углерод в его структурах связан практически полностью, находясь там в составе различных карбидов. Его очень легко отличить, на изломе он белый и блестящий. Обладает очень высокой твердостью, большой хрупкость и с трудом поддается обработке. Сварка белого чугуна затруднена, поскольку сопровождается образованием различных трещин во время нагрева и охлаждения.
- Половинчатые отбеленные чугуны. В отливке в верхнем слое он белый, в тоже время в сердцевине он серый и содержит в своей структуре большое количество графита. Он прочен, но в тоже время легче поддается обработке, менее хрупок.
- Серый чугун (СЧ). Содержание углерода в составе обычно составляет 3.5% . В составе очень много графита. Прочный, достаточно износостойкий, хорошо поддается обработке. Из серого чугуна изготавливают детали, работающие при отсутствии ударной нагрузки.
- Ковкий чугун (КЧ). В химический состав этого чугуна входит 1.4% кремния, 1% марганца. Углерод обладает хлопьевидной формой. Ковкий чугун получают из белого чугуна. Для этого выполняют его термическую обработку, то есть нагревают и выдерживают в этом состоянии в течении заданного времени. Эта операция называется томлением.
- Высокопрочный чугун (ВЧ) В структуре этого чугуна углерод обладает шаровидной формой. Их получают путем добавок в жидкий чугун магния, циркония в количестве 0.02% — 0.08% . Из высокопрочного чугуна изготавливают прокатные валики, кузнечнопрессовое оборудование, корпуса паровых турбин, коленчатые валы и другие ответственные детали, работающие при высоких циклических нагрузках и в условиях изнашивания.
Коррозионная стойкость чугуна зависит от его химического состава, структуры и чистоты .
Например, содержание кремния в чугуне до 7% отрицательно влияет на его химическую стойкость, а выше 11% положительно . Содержание марганца до 0.75% увеличивает химическую стойкость чугуна, а выше – уменьшает . Фосфор повышает стойкость чугуна против разрушения в щелочах и уменьшает в кислотах .
Легирование, модифицирование, сфероидизация графитовых включений способствует повышению коррозионной стойкости чугуна.
1.4. ЦВЕТНЫЕ МЕТАЛЛЫ И СПЛАВЫ
К цветным металлам и сплавам относятся практически все металлы и сплавы, за исключением железа и его сплавов.
Сплавы цветных металлов применяются для изготовления деталей, работающих в условиях агрессивной среды, подвергающиеся трению, требующих большой теплопроводности, электропроводности и уменьшенной массы.
1.4.1. МЕДЬ И ЕЕ СПЛАВЫ
Медь — металл красноватого цвета, отличается высокой теплопроводностью, электропроводностью, высокой пластичностью и стойкостью к атмосферной коррозии. Имеет низкую прочность.
Медь — малоактивный металл, в электрохимическом ряду напряжений она стоит правее водорода. Она не взаимодействует с водой, растворами щелочей, соляной и разбавленной серной кислотой. Однако в кислотах – сильных окислителях (например, азотной и концентрированной серной) – медь растворяется. Медь считается «благородным», мягким металлом и обладает хорошей коррозионной стойкостью при различных внешних условиях. Однако во влажной атмосфере, содержащей углекислый газ медь покрывается зеленоватым налетом основного карбоната меди.
Медь используется как в чистом виде, так и в виде сплавов:
-
-
- Латунь — сплав меди с цинком (от 10% до 40%). Хорошо поддается холодной прокатке, штамповке, вытягиванию. Латунь обладает коррозионной стойкостью в обычной атмосфере, а также в условиях морского климата. Латунь интенсивно корродирует под воздействием минеральных кислот (азотная, соляная). Серная кислота действует на латунь значительно медленней, однако в присутствии окислителей скорость коррозии увеличивается на два порядка. Латунь устойчива в растворах щелочей (за исключением аммиака) и в концентрированных растворах нейтральных солей. Сильное корродирующее действие на латунь оказывает сероводород . При этом латунь с повышенным содержанием цинка (более 30%) более устойчива в среде сероводорода, чем латунь с низким содержанием цинка.
-
Латунь подвержена особым видам коррозии:
-
- Обесцинкование – это особая форма коррозии, при которой происходит растворение поверхностных слоев латунного изделия в реагенте. Процесс обесцинкования наблюдается при контакте латуни с электропроводящими средами (кислые и щелочные растворы). В результате обесцинкования латунь становиться пористой, на поверхности появляются красные пятна. Малые добавки мышьяка, фосфора и сурьмы повышают устойчивость латуни к этому виду коррозии.
- «Сезонное» или межкристаллитное растрескивание – связано с воздействием соответствующей коррозионной среды (присутствие в атмосфере аммиака, сернистого газа, различных аминов, влажного диоксина углерода). Склонность к коррозионному межкристаллитному растрескиванию усиливается с увеличением (свыше 15%) содержание цинка.
- Бронза — сплав меди с оловом (до 10 %), алюминием, марганцем, свинцом и другими элементами. Обладает хорошими литейными свойствами. Из нее изготавливают вентили, краны, задвижки, люстры и другие изделия из литья. Бронза отличается значительной коррозионной стойкостью. Олово повышает эти свойства, а свинец ухудшает. Оловянная бронза стойка в горячих и холодных растворах серной кислоты (концентрированная кислота действует на них при высоких температурах), а также в холодных разбавленных растворах серной и фосфорной кислоты. На них не влияет уксусная, муравьиная, лимонная и др. органические кислоты. Растворы хромовой кислоты, щелочей и аммиака вызывают значительную коррозию. Бронза взаимодействует с влажным хлором, сероводородом, хлористым водородом и ацетоном. Они стойки к эфирам, спиртам, альдегидам.
- Мельхиор – сплав меди в основном, с никелем, иногда с добавками железа или марганца. Мельхиор отличается высокой коррозионной стойкостью в пресной и морской воде, сухих газах, а также в атмосферных условиях. С увеличением содержания никеля коррозионная стойкость, а также прочность увеличиваются.
Медные сплавы подвержены питтинговой коррозии. На латунных сплавах может возникнуть избирательная коррозия.
1.4.2. АЛЮМИНИИЙ
Алюминий — легкий серебристый металл. Обладает низкой прочностью при растяжении, низкой твердостью, низкой плотностью. Он стоек к атмосферной коррозии. В чистом виде применяется редко (краски, газообразователи, фольга). Для повышения прочности в алюминий вводят легирующие добавки (Fe, Mn, Cu, Mg, Si) и применяют некоторые технологические приемы
Алюминий обладает высокой коррозионной стойкостью в средах с Pн = 4,8 — 9,0. На воздухе на нем мгновенно появляется сплошная окисная пленка (0,01 – 0,02 мкм). На сплавах окисные пленки несплошные, так как содержат частицы посторонних металлов, способных ускорять коррозионные процессы.
Алюминий подвержен следующим видам коррозии:
- Сквозной
- Равномерной
- Межкристаллитной (особенно в сплавах Al – Cu)
- Коррозионной усталости (при нагрузке в коррозионной среде)
- Послойной (в сплавах с медью и магнием)
- Контактной (в контакте с более благородными металлами при наличии агрессивной среды)
Легирующие присадки меди, кремния, марганца, никеля, кобальта и железа снижают его коррозионную стой- кость, хотя и значительно улучшают механические свойства . Водород увеличивает пористость алюминия, а при- садки магния, наоборот, улучшают его коррозионную стойкость в растворах щелочей и хлоридов . В растворах хлоридов и бромидов пленка на алюминии не является стабильной. При сдвиге его потенциала в сторону положительных значений быстро наступает резкое увеличение тока, соответствующее пробою пленки . Стационарные потенциалы алюминия и его сплавов при увеличении рН морской воды сдвигаются в сторону отрицательных значений. Это явление в значительной степени влияет на процессы коррозии. В щелочах алюминий корродирует значительно за счет растворения оксидной пленки. Безводные жирные кислоты вызывают усиленную коррозию алюминия. Углеводороды на него не действуют.
Силумины — сплавы алюминия с кремнием (до 14% ) . Они обладают высокими литейными качествами, малой усадкой, прочностью, твердостью, но достаточно хрупкие при ударных нагрузках.
Дуралюмины — сплавы алюминия с медью (до 5.5%), кремнием (до 0.8%), марганцем (до 0.8%), магнием (до 0.8%). Их свойства улучшают термообработкой.
Алюминий и его сплавы имеют очень широкое применение практически во всех отраслях промышленности. В последнее время алюминиевые сплавы стали широко применяться в строительстве для несущих и ограждающих конструкций.
1.4.3. ТИТАН И ЕГО СПЛАВЫ
Титан и его сплавы в последнее время получили широкое распространение благодаря своим свойствам:
- высокой коррозионной стойкостью,
- меньшей плотностью по сравнению со сталью (намного легче),
- высокими прочностными свойствами,
- повышенной теплостойкостью.
На основе титана создаются легкие и прочные конструкции с уменьшенными габаритами, способные работать при повышенных температурах.
Титан стоек на воздухе и в морской воде, а также хорошо сопротивляется гидравлической кавитации и действию HNO3 любой концентрации, но в дымящей кислоте он подвержен коррозионному расстрескиванию. Титан не устойчив в соляной и плавиковой кислотах при повышенных температурах и сильно корродирует в горячих органических кислотах (щавельной, трихлоруксусной, муравьиной).
1.4.4. МЕТАЛЛИЗАЦИЯ ПОКРЫТИЯ
Одним из действенных методов защиты от коррозии является металлизация конструкции, т.е. нанесение на стальную поверхность металлоконструкции другого более коррозионно-стойкого металла (хромирование, цинкование, алюминирование пр.).
1.4.4.1 ЦИНКОВАНИЕ
Цинковые противокоррозионные покрытия нашли наибольшее применение среди металлических покрытий в связи с довольно высокими защитными свойствами цинка в нейтральных и слабощелоч¬ных средах, а также вследствие относительной простоты и невысокой стоимости его нанесения. По данным, представленным в ГОСТ 9. 104—2018, можно судить о скорости коррозии низкоуглеродистой стали и цинка в аналогичных условиях
св. 0,7 до 5Категория коррозионной активности | Потери массы на единицу поверхности/потеря толщины (после первого года воздействия) | |||
---|---|---|---|---|
Низкоуглеродистая сталь | Цинк | |||
потери массы, г/м2 | потери тощины, мкм | потери массы, г/м2 | потери тощины, мкм | |
С1 очень низкая | до 10 включ. | до 1,3 включ. | до 0,7 включ. | до 0,1 вкл |
С2 низкая | св. 10 до 200 | св. 1,3 до 25 | св.0,7 до 5 | св.0,1 до 0,7 |
С3 средняя | св. 200 до 400 | св. 25 до 50 | св. 5 до 15 | св.0,7 до 2,1 |
С4 высокая | св. 400 до 650 | св. 50 до 80 | св. 15 до 30 | св.2,1 до 4,2 |
С5 очень высокая | св. 650 до 1500 | св. 80 до 200 | св. 30 до 60 | св.8,4 до 4,2 |
СХ крайне высокая | св. 1500 до 55000 | св. 200 до 700 | св. 60 до 180 | св. 8,4 до 25 |
Имеются две основные причины широкого применения цинковых покрытий. Первая — высокая при¬родная стойкость цинка в атмосферных условиях, и вторая — анодное поведение цинка по отношению к стали, т.е. возможность защитить его катодно. Во втором случае цинк, находящийся на поверхности стали, растворяется, защищая при этом основной металл.
Методы нанесения цинка на поверхность описаны ниже. Выбор того или иного метода нанесения цинка опре- деляется требованиями к покрытию, эксплуата¬ционными факторами, условиями нанесения и экономическими аспектами.
Защищаемая поверхность перед нанесением покрытия должна быть очищена путем абразивной обработки и обдувки чистым сжатым воздухом.
1.4.4.2 АЛЮМИНИРОВАНИЕ
В промышленных и морских условиях скорость коррозии алюминия примерно в три раза меньше скорости коррозии цинка, причем коррозия уменьшается со временем благодаря образованию на алюминии плотной пленки оксидов с хорошими барьерными свойствами и адгезией. В контакте со сталью алюминиевое покрытие является анодным.
Алюминий обладает высокой коррозионной стойкостью в средах с Pн = 4,8 — 9,0 . На воздухе на нем мгновенно появляется сплошная окисная пленка (0,01 – 0,02 мкм).
На сплавах окисные пленки несплошные, так как содержат частицы посторонних металлов, способ¬ных уско- рять коррозионные процессы .
Алюминий подвержен следующим видам коррозии :
- Сквозной
- Равномерной
- Межкристаллитной (особенно в сплавах Al – Cu)
- Коррозионной усталости (при нагрузке в коррозионной среде)
- Послойной (в сплавах с медью и магнием)
- Контактной (в контакте с более благородными металлами при наличии агрессивной среды)
- Коррозионная устойчивость выше, чем при электролитическом цинковании.
- Вредное производство, большие энергозатраты.
- высокая производительность;
- получение достаточно высокого уровня защиты изделий;
- равномерностью покрытия без потеков, капель, с сохранением формы и размеров изделия;
- получение декоративных защитных покрытий (гладких, блестящих),не требующих дополнительной обработки.
- Идеальное сцепление (адгезия) изделий, на которые наносят защитный слой, с цинковым покрытием.
- Экономичность технологии (ее себестоимость относительно невысока, так как требуются небольшие площади для выполнения операции, малые затраты рабочей силы и энергии); Обеспечение абсолютно ровного диффузионного покрытия, которое обладает высокими антикоррозионными показателями. Защитные свойства в 5 раз выше, чем при электролитическом цинковании, в 1,5-2 раза – чем при горячем цинковании;
- Идеально для метизов с резьбой;
- Токсическая, химическая и экологическая безопасность;
- Низкая производительность. Небольшие размеры изделий. Низкая эстетика.
Легирующие присадки меди, кремния, марганца, никеля, кобальта и железа снижают его коррозионную стойкость, хотя и значительно улучшают механические свойства. Водород увеличивает пористость алюминия, а присадки магния, наоборот, улучшают его коррозионную стойкость в растворах щелочей и хлоридов. В растворах хлоридов и бромидов пленка на алюминии не является стабильной. При сдвиге его потенциала в сторону положительных значений быстро наступает резкое увеличение тока, соответствующее пробою пленки. Стационарные потенциалы алюминия и его сплавов при увеличении рН морской воды сдвигаются в сторону отрицательных значений. Это явление в значительной степени влияет на процессы коррозии. В щелочах алюминий корродирует значительно за счет растворения оксидной пленки. Безводные жирные кислоты вызывают усиленную коррозию алюминия. Углеводороды на него не действуют.
Алюминиевые покрытия предпочтительнее цинковых в нейтральных и слабокислых средах и уступают им в щелочных средах. Во многих случаях хорошие результаты дает легирование алюминия цинком (5-35%) при различных методах нанесения покрытий.
1.4.4.3 МЕТОДЫ МЕТАЛЛИЗАЦИИ
Можно выделить 4 основных способа металлизации.
1.4.4.3.a ТЕРМИЧЕСКОЕ НАПЫЛЕНИЕ АЛЮМИНИЯ, ЦИНКА И ИХ СПЛАВОВ (THERMaLLY SPRaYED SURFaCES).
Термически напыленные поверхности представляют собой сталь, покрытую цинком, алюминием или их сплавами путем газотермического или электродугового напыления в соответствии с ISO 2063 (все части). Метод также называется шоопированием (по фамилии швейцарского инженера Макса Шоопа, запатентовавшего газопламенный метод напыления в 1913 году).
Принцип действия: стержневой присадочный материал с помощью механизма подачи направляется через центральное отверстие горелки в высокотемпературную зону пламени, где нагревается до температуры плавления. Полученная капля жидкого металла с его торца распыляется сжатым воздухом и в виде мелких частиц переносится на поверхность детали.
Используют проволочный (прутковый) и порошковый металлизатор.
Этим методом можно напылять покрытие на ограниченные участки крупногабаритных изделий, а также покрывать большие металлоконструкции как в заводских условиях, так и на месте их монтажа, при минимальных затратах на оборудование и оснастку. У нас метод регламентируется следующими стандартами:
ГОСТ 9.304-87 «Покрытия газотермические. Общие требования и методы контроля»
ГОСТ 28302-89 «Покрытия газотермические защитные из цинка и алюминия металлических конструкций. Общие требования к типовому технологическому процессу».
Алюминий и цинк – анодные покрытия по отношению к железу. Алюминиевое ПК более дешевое, но требует лучшей подготовки поверхности.
Теоретическая часть: для создания защитного покрытия минимальная толщина цинкового напыления -25 мкм, алюмининиевого – не менее 75 мкм. Цинковые Пк для pH 6-12, алюминий – от рН 3,5 и выше.
Преимущества
Преимуществом этого метода по сравнению с другими методами цинкования является простота технологии и высокая скорость нанесения покрытия, в том числе толстослойных и многослойных, а также возможность работы в полевых условиях, относительно невысокая температура нагрева поверхности (не более 1500С), высокая прочность сцепления (до 280 МПа). Данное покрытие является пористым и рекомендуется перекрытие ЛКМ.
Существует два принципа расплавления металла: электродуговой (более современный, но пока не имеет широкого распространения) и газопламенный (кислород + ацетилен, более распространенный, проще для эксплуатации).
Метод газопламенного напыления прекрасно подходит для обработки труднодостижимых участков. Метод электродугового напыления применяется, обычно, для больших участков (стационарные установки). Стационарный (механизированный) – в поточных линиях цинкования металлоконструкций, проката и труб и ручной. За один проход – от 10 до 200 мкм. Можно наносить несколько слоев. Ручной метод напоминает нанесение обычным окрасочным пистолетом.
1.4.4.3.B ГОРЯЧЕЕ ЦИНКОВАНИЕ (HOT-DIP-GaLVaNIZED SURFaCES).
Горячеоцинкованные поверхности представляют собой сталь, покрытую цинком или цинковым сплавом путем погружения в ванну расплава в соответствии с ISO 1461 или ГОСТ 9.307-89 (ИСО 1461-89) «ЕСЗКС. Покрытия цинковые горячие. Общие требования и методы контроля». Метод впервые описан в 1742 году, промышленный патент – в 1836 году ( Франция).
Металлоконструкции длиной до 12 м погружаются в ванну с горячим цинком (460 0С). Оптимальная толщина 80-120 мкм, возможно от 40 до 250 мкм (для крупных деталей). Полученное покрытие отличается превосходным внешним видом, однако его нельзя наносить на резьбовые соединения.
Достоинства:
Недостатки:
1.4.4.3.C 3. ЭЛЕКТРОЛИТИЧЕСКОЕ (ГАЛЬВАНИЧЕСКОЕ) ЦИНКОВАНИЕ
Недостатки:
1.4.4.3.C 3. ЭЛЕКТРОЛИТИЧЕСКОЕ (ГАЛЬВАНИЧЕСКОЕ) ЦИНКОВАНИЕ
< Zinc-electroplated surfaces> Цинк-гальванические поверхности состоят из стали, покрытой электрохимически осажденным цинком. Отправная точка промышленного применения – 1838 г. (ровесники с горячим цинкованием). ГОСТ 9.301-86 «ЕСЗКС. Покрытия металлические и неметаллические неорганические. Общие требования» Этот метод цинкования самый распространенный, достигает наилучших декоративных качеств. Гальваническое цинкование представляет собой электролитический метод нанесения тонкого защитного слоя цинка на изделие (медный анод (+) и изделие (-) погружены в раствор электролита). Процесс происходит при обычной температуре, поэтому, кроме очень узкой переходной области, в системе не наблюдается железо-цинковых сплавов, и адгезия цинкового слоя к металлу основы относительно невелика. Толщина покрытий 5–40 мкм.
Достоинства:
Недостатки: Низкая адгезия образуемого покрытия с изделием, требующая особой тщательности подготовки (очистки) поверхности последнего. Вероятность водородного охрупчивания изделий. Образование ядовитых и вредных для окружающей среды отходов, которые необходимо подвергать тщательной очистке. Не может конкурировать с методом горячего цинкования при защите цинком крупных и средних деталей.
1.4.4.3.D ТЕРМОДИФФУЗИОННОЕ ЦИНКОВАНИЕ. SYN. ШЕРАРДИЗАЦИЯ
Назван по фамилии английского изобретателя — Шерард Купер-Коль, 1900 г.). < Sherardized surfaces>
ГОСТ Р 9.316-2006 «ЕСЗКС. Покрытия термодиффузионные цинковые. Общие требования и методы контроля.»
Шерардизированные поверхности представляют собой сталь, покрытую слоями цинкового сплава, полученную при нагревании стальных деталей в контейнере вместе с цинковой пылью.
Метод заключается в нагревании (при 350—430 °С) стальных изделий в порошке цинка для получения диффузионного поверхностного слоя. Производится во вращающемся или качающемся герметичном контейнере. Толщины покрытия – от 5 до 50 мкм.
Достоинства:
Недостатки:
Преимущества и недостатки перечисленных методов можно свести в следующую таблицу.
Метод металлизации | Термическое напыление алюминия, цинка и их сплавов | Горячее цинкование | Электролитическое (гальваническое) цинкование | Термодиффузионное цинкование (шерардизация) |
---|---|---|---|---|
Ручное нанесение | да | нет | нет | нет |
Толщины | 10 до 200 мкм | 40 до 250 мкм | 5–40 мкм | 5 до 50 мкм |
Декоративные свойства | средние | средние | отличные | ниже среднего |
Крупные детали | нет | да | да | нет |
Защитные свойства | хорошие | среднее | ниже среднего | отличные |